Tech & Process
Delivering the Cutting edge
While continuously investing in the latest technology is expensive, it remains an essential effort in continuously improving efficiency and optimizing data collection and processing procedures. Ever-evolving technology in sensors and software, coupled with proven aircraft, have helped the industry provide better data quicker and at a lower cost.
Whether in the private or public sector, our clients require premium products based on three factors: quality, schedule, and price. To meet our clients’ needs our objective is to:
- Ensure that the quality of our work is validated at every step of production
- Cross-train staff to ensure depth of skill and flexibility among our workforce
- Maintain plenty of aircraft, sensors, other assets and staff to provide proper acquisition and processing capacity
- Maintain contingency plans for every potential variable, from weather to illness to disaster planning to data backup
- Manage your project carefully to ensure that delivery milestones, project specifications and accuracy standards are all met
- Continuously refine our production processes through our R&D department, which provides quality improvements, cost savings, and expedited schedules to our clients
In our ongoing effort to maximize efficiency, our IT staff provides continuous improvements to processing and automation, resulting in increased speed and an unmatched client satisfaction rate.
Our QA & QC processes comply with ISO 9001:2008 international standards. These measures enable us to systematically identify and eliminate inefficiencies in our production processes, reducing project completion time while optimizing the quality of our products and the integrity of the data. This approach to process improvement enables Surdex to produce data faster while reducing the amount of error, resulting in exceptionally reliable data that integrates into our clients’ systems smoothly and functions precisely as intended.
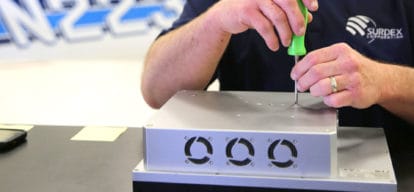
Project Management
A successful project management strategy not only keeps our clients’ projects on schedule, it also keeps them apprised of progress of all activities. During project planning, the optimal acquisition design is developed, and sufficient control is calculated to ensure accuracy standards are met. Project status is related routinely using both graphical and textual reporting, from acquisition to production to delivery.
If an issue becomes evident to Surdex, our project managers will take the following course of action:
- Inform the client that an issue has arisen and define the situation
- Develop a set of suggested solutions or actions, consulting internal resources and experts
- Convey the suggested solutions or actions to the client for discussion and approval
Aerial acquisition is in most cases reported daily; on larger projects, Surdex even provides an online flight tracking tool that uses GPS and a satellite uplink to report an assigned aircraft’s real-time location and status of acquisition.
These efforts provide clients with a great deal of assurance that their project is being properly managed, and that any irregularities are caught quickly and corrective action taken immediately. As a result, most projects avoid significant issues – and the associated delays for corrections – yielding better adherence to schedules.
Download and read more about our Project Management.
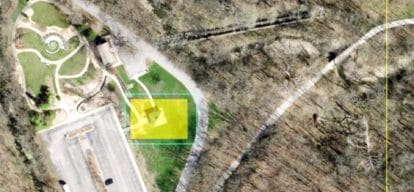
SurCheck
Surdex’s commitment to continuous improvement and unrivaled efficiency firmly establishes us as a leader among geospatial data providers. Our commitment to delivering a premium quality product is reflected in the fact that 98% of our data is accepted by clients on delivery.
To give our clients the ability to quickly and efficiently inspect and validate their imagery, Surdex developed a web-based tool called SurCheckSM This easy-to-use, intuitive interface enables users to:
- Inspect data
- Identify areas requiring remediation
- Validate that corrections have been made
Many of our clients on even large projects conclude that our internal QC is so robust, they may have only a handful of corrections.
Download and read more about our SurCheck online inspection tool.
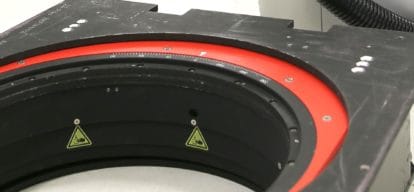
Imaging & LiDAR Sensors
We have always invested in top-of-the-line imaging equipment because imaging is at the heart of all mapping projects. Our sensors provide excellent image resolution and color quality. All sensors are equipped with ABGPS, IMU and the latest forward motion compensation technology and provide high quality, accurate stereo imagery to meet the needs of our customers.
- Leica ADS 100 Aerial Digital Sensors (5): These “pushbroom” sensors are among the most sophisticated systems on the market today. They acquire imagery in a continuous strip with each flight line. With the widest swath of any sensor on the market, they offer reduced acquisition time and have excellent image quality.
- Leica DMC-1 Digital Frame Cameras (4): The DMC-1 is a frame camera utilizing pan-sharpening to blend full-resolution panchromatic images with lower-resolution multispectral (red, green, blue, near infrared) images. A longtime industry workhorse, the DMC-1 is a tried-and-true system that provides exceptional image quality and cost efficiency.
- Phase One Digital Camera (2): The Phase One frame cameras can be collocated with the Galaxy LiDAR sensor for simultaneous LiDAR and imagery acquisition. This is an ideal configuration for smaller projects requiring both products, providing increased efficiency because collection can be completed in one flight rather than two.
- Leica RCD30 Oblique Camera System (1): This system is specifically designed for high-accuracy 3D urban mapping and 3D corridor mapping applications. It can be co-mounted with our Galaxy LiDAR sensor for simultaneous LiDAR/image capture.
- Teledyne Optech Galaxy lidar sensors (3): Among the most advanced and efficient lidar sensors available today, the Galaxy uses innovative lidar technology enhancements and incorporated flight and calibration software that significantly increase sensor performance and collection efficiency, improve data quality, and greatly simplify the collection process.
Download and read more about our imaging and lidar sensors.
Our Process
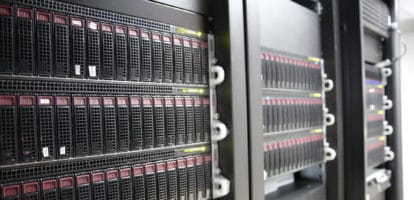
Key Performance Metrics
To ensure we continuously improve our processes, we measure key performance values to assure our clients of optimal performance. Our key performance metrics make us a top performer, as rated by our customers:
- 98% First-Time Acceptance
- 98% On-Time Delivery
- 99% Client Satisfaction
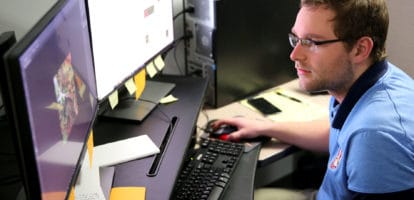
First-Time Acceptance
Our rigorous internal QA/QC measures assure our clients that they are receiving premium quality products. Our clients spend less time reviewing and managing corrections, which in turn means their products are put into operation more quickly. 98% of our data is accepted by clients on the first delivery.
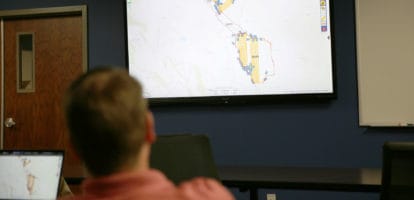
On-Time Delivery
We understand that our clients depend on us delivering their data on time so that they can achieve their own goals. In an industry where delays are normal, we are committed to delivering on schedule. We achieve this by:
- Understanding exactly how much time a project requires
- Maintaining a reserve workforce
- Having a very large production capacity
- Having cross-trained staff who can provide contingency labor
- Never over-promising
As such, Surdex averages a 98% on-time delivery record.
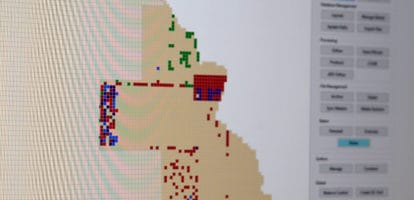
Client Satisfaction
One of our most important measures is client satisfaction. This takes into account not only the quality of the deliverables and adherence to schedules, but also how well we served our clients:
- Did the level of communication meet your needs?
- Was your project manager responsive to inquires?
- How well did we manage and resolve any issues that arose?